Mechanical processes
Polishing
High-quality spindle drives with individually adjustable speed for optimum polishing of the workpiece.
Lapping
Ultrasonic-assisted lapping and polishing process for small parts.
Internal polishing
With special processes, the internal surface of straight, normal and reduced tubes can be improved.
With these processes, an excellent surface quality can be achieved depending on the starting material.
Vibratory finishing
The workpiece is placed in a container with grinding wheels. Oscillating motions cause the edges and rough surfaces to be removed, thus improving the surface quality.
Sand and glass pearl blasting
For deburring, roughening, structuring or matting surfaces. Depending on the requirements, various blasting media and setting parameters are possible.
Chemical processes
Electropolishing
Process
Electropolishing is an electrochemical removal process with an external power source. In an electrolyte specially adapted to the material, the material is anodically removed from the workpiece to be machined.
This means that the metallic workpiece forms the anode in an electromechanical cell. The metal prefers to dissolve on uneven surfaces due to tension peaks. The removal of the workpiece is carried out without stress.
Applications
Reduction of surface roughness, improvement of surface corrosion resistance, fine edge rounding.
Electropolishing can only be applied to the outer surfaces of the cannulas.
The part size is limited to max. 500 x 500 mm.
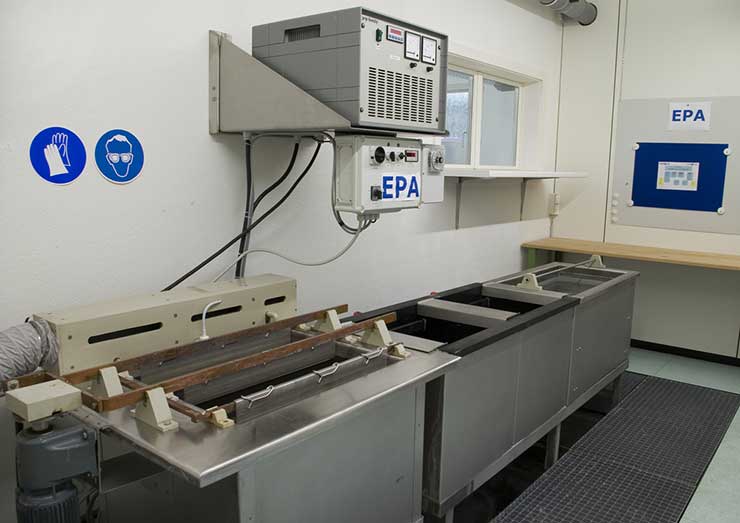
Topography
- Change of adjacencies due to load-free material removal
- Significant reduction of roughness and area ratio factor f through targeted micro-smoothing
- Increase of the gloss level
Morphology
- Removal of all damaged surface layers through targeted, load-free material removal to the undisturbed, pure austenite phase
- Formation of a passive protective layer rich in chromium oxide
Energy level
- Reduction of the surface tension to the specific material characteristic value of austenites
Properties of electropolished surfaces
- Smooth, glossy surface
- Metallically pure
- High corrosion resistance
- Optimum cleaning behaviour
- Easy to weld and solder
- Deburred in the micro range
Passivation
Process
Passivation is the specific chemical production of a chromium oxide layer to prevent oxidation or corrosion of the freshly processed stainless steel.
The chromium oxide layer is created by the oxidation of the chromium ions in the stainless steel. This natural process of chromium oxide build-up requires several hours in ambient conditions, but can be accelerated by the use of chemicals. The passive layer is a regenerating (self-healing) layer. The layer thickness is 1-3 nm.
The passivation of the inner and outer surfaces of hollow needles and cannulas is one of our standard processes.
Ultrasonic cleaning
Wet chemical cleaning with ultrasonic support is a modern and very effective technology. The longitudinal waves of the sound create cavities in the liquid which knock off dirt particles from the surface.
In our multi-stage ultrasonic cleaning system, all parts are also cleaned between the individual work steps. A final rinse is carried out with deionized water. For example, we use a structure specially designed for the internal and external cleaning of hollow needles. A continuous exchange of liquids takes place inside the tubes. Working with several ultrasonic frequencies makes it possible to adapt the cavities of the sound to the part contamination.
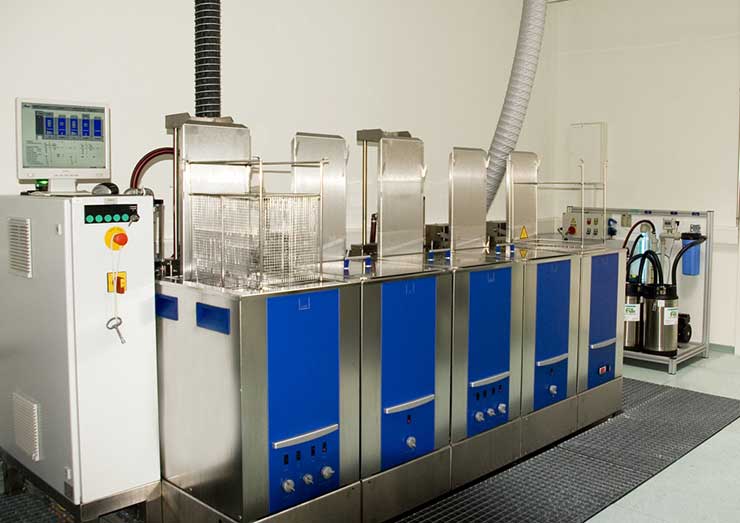